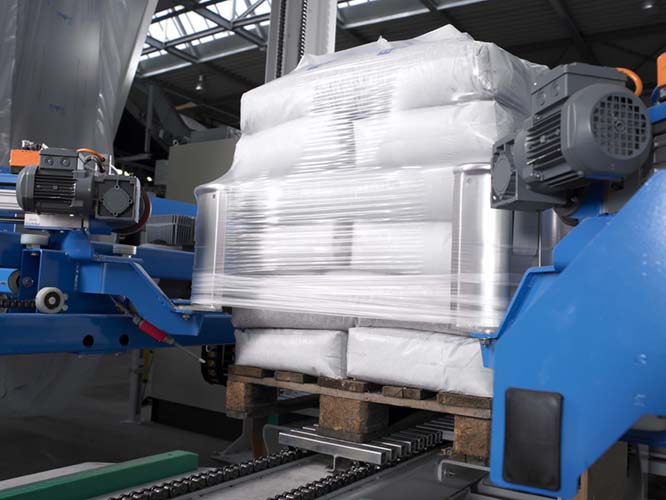
Stretch hood film packaging uses a tubular elastic plastic film that is heat-sealed at the top. It is stretched horizontally and transversely at room temperature. It is vertically covered from the top of the package and released at the bottom of the tray to tightly wrap the product. A packaging method, also known as cold shrink film packaging, cold stretch film packaging, etc. Stretch hood films are usually made of thermoplastic elastomer materials, the flexible polymer chains of which are rubbery polymers forming a cross-linked network. When the elastic sleeve is stretched, the polymer chains stretch and deform greatly, but slippage between polymer chains does not occur, stress resisting deformation is generated inside the polymer, and the entropy value decreases to form an unstable system. When the tensile force is released, the elastic hood deforms and recovers under the action of stress, and the polymer chains return to their original curled state, causing the hood to shrink and press tightly against the packaging.
Stretch hood film packaging technology was developed on the basis of heat shrink film packaging and stretch packaging. It was first developed by the Danish company Lachmeier in the 1980s and produced the world’s first machine in 1988. Fully automatic stretch hood film packaging equipment. Stretch hood film packaging absorbs the advantages of traditional heat shrink film packaging and stretch packaging. It has low cost, high efficiency, complete packaging, high safety, good transparency and physical protection properties. It is widely used in food, household Electrical appliances, chemicals and construction industries. This next-generation stretch film is cost-effective and improves load protection for palletized merchandise while providing superior transparency for store product displays.
Lachmeier Packaging Machinery Equipment Co., Ltd. manufactured the world’s first cold stretch hood film packaging equipment, and then continued to improve and enrich this technology. Its stretch hood equipment mainly includes single film frame and multi-film frame models. Users can Choose according to the size of the pallet. Lachmeier Power Flex T1 stretch hood equipment is a newly launched model. It has a unique vacuum/mechanical film opening system, hydraulic stretching device, and encoder to control the pulling position, and can monitor the quality throughout the process. Increase the visual effect of the product.
Stretch Hood Film Packaging Working Process
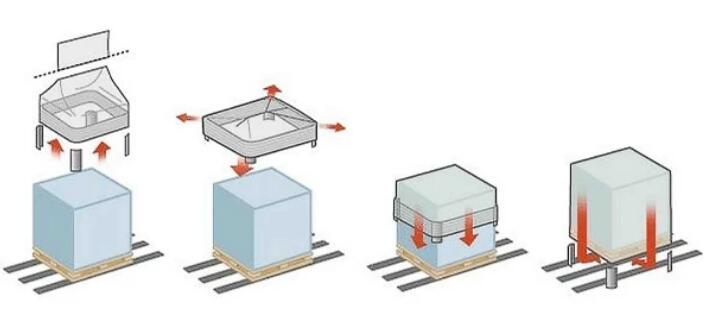
After the pallet is loaded with goods, the pallet is placed on the stretch hood film packaging equipment. The data processing system of the packaging equipment calculates the exact length of the required stretch hood film based on the measured information. Once the unwinding reaches the limit length, the packaging equipment The top of this section of film is sealed and the film roll is cut. A separate drive then releases the stretch film roll and secures it in place. Four mechanical stretching arms clasp the four corners of the elastic hood and unfold it against the adhesion force of the film. This requires that the inner side of the elastic hood has a certain degree of openability, while ensuring the uniformity of the adsorption force of the mechanical stretching arm on the film and the uniformity of its unfolding speed. Then four mechanical stretching arms are inserted into the open elastic film tube from below and stretched horizontally and transversely to the four corners (if an appropriate resin formula is used, the film stretching rate can be increased to more than double the original). After it is ready, the stretching frame and the stretching arm move downward, so that the elastic hood is stretched in two directions to cover the packaging pallet. This process is key to the final quality of the packaging. If the stretch arm is not positioned correctly, wrinkles will appear in the elastic hood and different packaging qualities will appear on the four surfaces of the pallet. When the film is stretched beyond the size of the pallet, the robot enters the bottom of the pallet and separates from the elastic hood. The film quickly shrinks and returns to its original state, thereby tightly clamping the packaging pallets together. The smaller the size of the original elastic hood, the greater the clamping force on the packaging. Finally, the robot is lifted again, and the packed pallets are transported away from the stretch hood film packaging equipment and stored in the warehouse ready for shipment.